Company
The Gattoni Rubinetteria brand is today synonymous withMade in Italy design and exclusive quality all over the world.
In over sixty years of existence, it has been able to establish itself on the national and international scene of the industry, developing prestigious collaborations with qualified designers, signing efficient products with an unmistakable style.
Green
By improving processes at all stages of production, Gattoni can produce taps that encourage responsible water consumption management.
Through the careful choice of suppliers, raw materials and workers, it also reaffirms its commitment to the environment and the supply chain of the partners with whom it deals, right up to the end consumer.
Company
Gattoni's entire production process takes place within the company's own factories, with a constant focus on quality and environmental impact.
1. Research and development
Qualified engineers take care of the design of new products, from conception to development, through the use of modern three-dimensional design software.
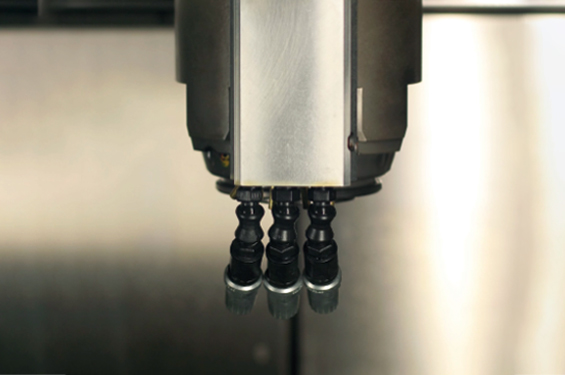
2. Testing laboratory
Where the technical tests necessary for the development of new products take place in order to obtain and maintain national and international certifications.
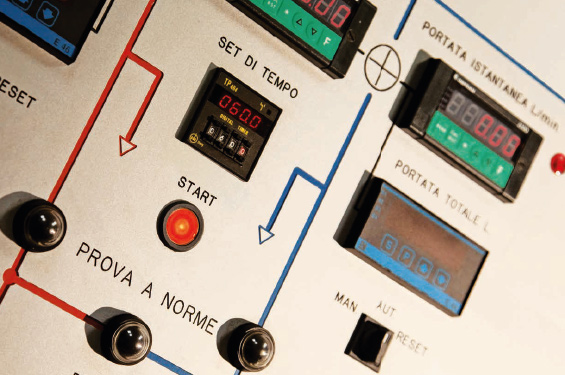
3. Certified raw materials
BLUEWAVE® is a new, fully lead-free alloy that complies with the latest regulations on lead content and is environmentally friendly.
Each production batch is accompanied by a certificate of analysis attesting to its conformity.
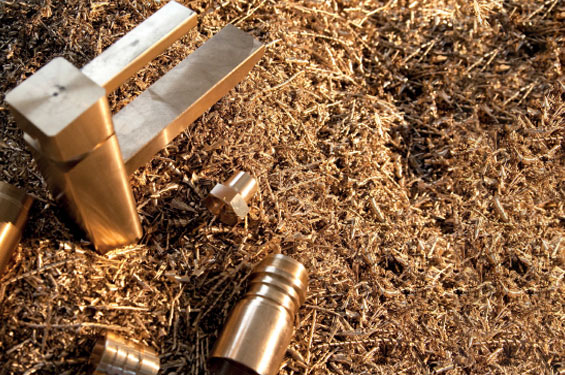
4. Foundry, printworks and turning
Our departments guarantee flexibility and precision thanks to state-of-the-art machinery and robots and a modern production organisation (Lean Manufacturing).
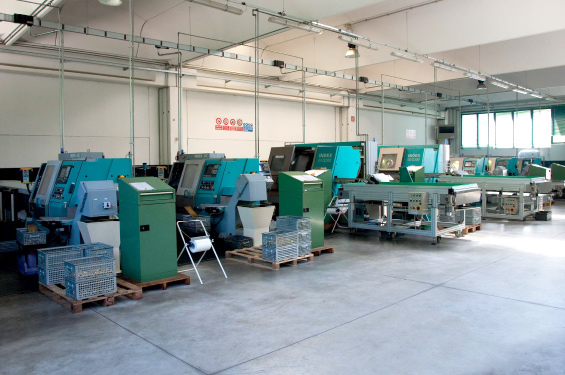
5. Cleaning
A state-of-the-art robotised department provides grinding, cleaning and polishing, ensuring high standards of quality and surface uniformity.
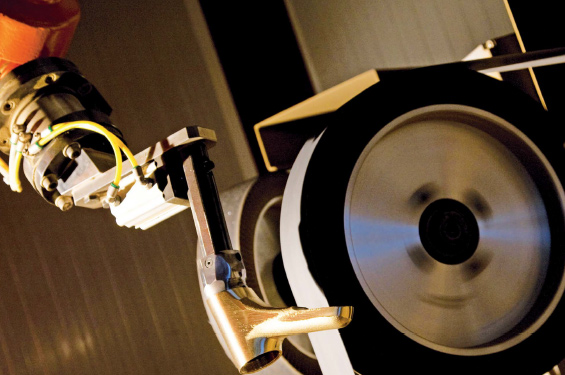
6. Galvanic
Chrome plating is carried out according to the patented PWP – Pure Water Process system that inhibits the release of toxic metals into drinking water.
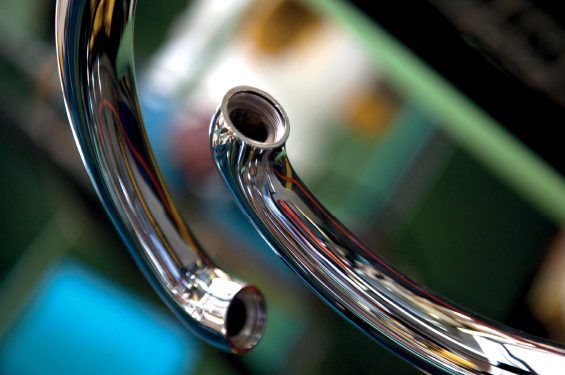
7. Sewage treatment plant
The modern chemical-physical purification plant ensures full compliance with all environmental protection laws and regulations.
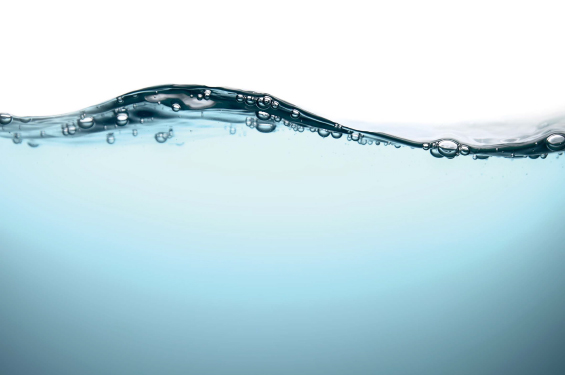
8. Painting
The use of the best products and treatments, allows to obtain high standard finishes, with resistance to salt spray tests exceeding 300 hours.
The use of the best products and treatments results in high standard finishes, with salt spray test resistance exceeding 300 hours.
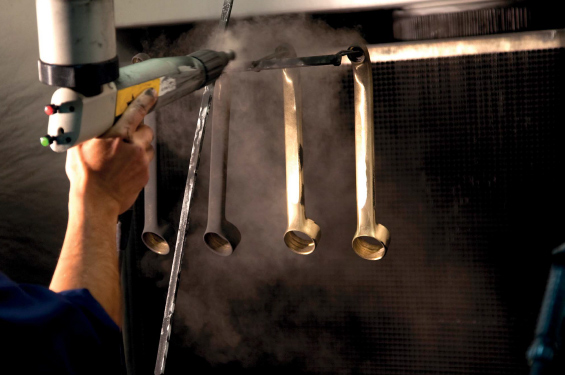
9. Assembly
Qualified personnel take care of the assembly and control of the entire production through test and inspection machines designed by the technical department.
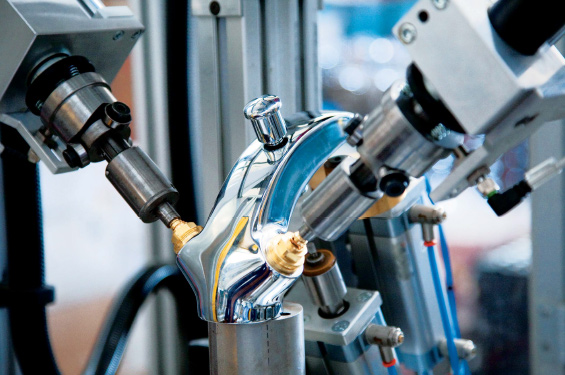
Sustainable innovation
Gattoni Rubinetteria has adopted guidelines to protect health, safety and the environment to be already today – and continue to be in the future – increasingly prepared, innovative, cutting-edge.
PHOTOVOLTAIC ENERGY
80% of the company’s total energy needs are covered by a state-of-the-art photovoltaic system: all production machinery and lighting are powered by self-generated energy, drastically reducing costs while emitting very low CO₂ emissions into the atmosphere.
LOW ENVIRONMENTAL IMPACT
Each stage of the production process is constantly monitored. In particular, the chrome plating phase in the galvanic bath takes place according to a system – the PWP (Pure Water Process) – that inhibits the release of toxic metals, such as lead or nickel ions, into drinking water.
CERTIFIED RAW MATERIALS
BLUEWAVE® is a new, fully lead-free alloy that complies with the latest lead content regulations and is environmentally friendly.
Each production batch is accompanied by a certificate of analysis attesting to its conformity.
RESPONSIBLE DESIGN
The new cartridges, the tap’s small beating heart, optimise consumption and avoid unnecessary overloading. Flow reducers at the end of the spout save up to 30% water. All soft rubber components and fittings are manufactured from non-toxic polymers.
RECYCLABLE PACKAGING
All Gattoni packages are made of cardboard, an easily recoverable and recyclable material. Inside, to protect the tap during transport, there is a sponge packaging, which has replaced the previous polystyrene packaging.